|
Technology
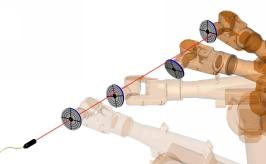
iSiOS uses the native precision of the laser
The patented functional
principle of iSiOS
is based on scanning some precisely straight laser beam with the robot.
When the robot hand is moved along the laser beam, smallest deviations
from the straight line are detected easily. Measurements of these
deviations yield a precise model of the robot by
elaborate mathematical algorithms. The identified robot model contains
all entities which influence the position of the robot hand.
Deformations of the robot arm, zero offsets of the joints or
gravity-induced displacements of the hand are compensated completely
and sustainably in the whole workspace.
iSiOS uses this principle usually
in reverse set-up: the compact, light-weight laser is carried by the
robot and stationary sensors are placed near the workcell
boundary.
Accuracy
Small
errors of the robot are mapped in full size onto the sensor over the
whole range of the laser beam. This is the foundation of the
conceptually
high sensitivity and precision of the system, which could easily be
increased further if
needed - e.g. for the calibration of micro-mechanisms. With two or
three
sensors placed and distributed properly on the boundaries of
the workcell, iSiOS calibration provides
maximum
robot positioning accuracy throughout the complete workspace.
The fundamentally new approach yields decisive technical
advantages
which were reserved to costly laser trackers before
- The large errors caused by gravitation-induced elasticities
and deflections are identified and
compensated precisely. This feature is a key component of the
superior absolute robot accuracy provided by the iSiOS
calibration
system.
- The appropriately sized, patented iSiOS
carbon fiber
etalon with two cost-efficient sensors yields sufficient error
dampening to determine absolute robot lengths precisely in contrast to
measurements
within a restricted area or at a single spot or at
some single calibration-object which may be used by
other approaches.
- During set-up, iSiOS does not
require the use of an additional laser tracker anymore, which was
needed up to now to measure the exact poses of obligatory
calibration-objects w.r.t the robot whenever demanding precision goals
had to be
met.
- iSiOS is highly sensitive also to orientational
errors. When the laser is mounted on the robot hand or tool, the laser
beam functions as an immaterial lever, which amplifies orientation
errors
proportional to distance, yielding maximum orientational accuracy after
calibration.
In
all its accuracy statements, Isios always takes the user defined
tooltip (TCP) into account. As an example, for certain
types of universal, industrial 6-joint robots, absolute positioning
errors at the tip of a tool of 200 mm length can be kept below 0.25 mm
in the whole
workspace including arbitrary changes in the joint-configuration (i.e.
shoulder left or right, elbow up or down, handflip).
Depending
on type, the average overall accuracy
of industrial
robots with workspace radius below 3 m and payload below 500 kg can be
raised up to the exceptionally high level of 0.3 mm and better. The overall
accuracy is the
effective accuracy at the workpiece when the hand pose is specified relative
to the workpiece only. In this case, the absolute pose of the hand
with respect to the world is unknown beforehand but is automatically
identifed by the iSiOS system with the
calibrated robot.
Cost-efficiency
The outstanding scalable sensitvity and high resolution of the system
is founded in the technological concept of the system, not in costly
measurement equipment.
Control of the calibrated robot
Once the parameters of the robot model are identified exactly, the
robot can be controlled exactly. This only requires appropriate
calculations before each
precision move of the robot - the so called
inverse transformation - but no additional measurements during
runtime. Calculation can be executed by the robot control unit. To
obtain superior robot accuracies the extremely
fast iSiOS realtime-precision-control module
is used which may be executed on the robot controller or independently
on a
remote computer.
Compare iSiOS
- iSiOS does not need elaborate,
sensitive optics or precision measurement devices. The scalable
sensitivity of the system and its particular technological concept
guarantee maximum
robot accuracy within the complete workspace - not only for typical
articulated-joint robots but also for cartesian robots, SCARA-robots
and special purpose gantry mechanisms with combinations of rotary and
prismatic (linear) joints.
- All compact components of iSiOS
inline calibration systems remain
installed in the workcell and are readily available when needed. Only
the stationary installation
of all components enables features like
- instant, synchronous
error-diagnosis of all robots of a production line within a
matter of minutes,
- permanent monitoring of all production devices including
mechanisms like rotary tables,
- automatic recalibration and restoration of maximum accuracy
after minor collisions or exchange
of robots within approx. 5 minutes, or
- compensation of wear and tear or temperature effects
concurrent with production.
- Robustness and compactness as well as contactfree, seamless
integration and function in rough obstructed
environments and under low visibility conditions are decisive
advantages in demanding industrial applications.
- The system redeems a large part of its cost already during
set-up and initial calibration of the original production line or
workcell, resp. Teach-In costs become obsolete. iSiOS
is laid out and priced for fast amortisation of stationary
installations in all accuracy-critical cells of a production line.
Compare accuracy, advantages and cost
Are you planning benchmark tests? Isios appreciates to support a
critical evaluation of iSiOS features and
resulting robot
accuracy as well as comparative tests with other calibration
principles.
|
 |