|
Synopsis
Robot calibration, cell calibration and 6D object
identification
iSiOS offers four lines of products:
- Depending on
the robot
type iSiOS
standard calibration raises the absolute positioning
accuracy of industrial robots up to
average errors below 0.25 mm. In some demanding applications of the
automotive industry, iSiOS-calibrated
special purpose robots are used e.g. as flexible measurement
systems (FMS) or coordinate
measurement
machines (CMM) resp. with a minimal average error after calibration.
- iSiOS inline calibration systems
are installed stationary in all workcells of a production line with
substantial
accuracy requirements. iSiOS
keeps Robots continually
on maximum precision
levels. The system monitors production accuracy and promptly
recalibrates the robot automatically or on demand. Optionally,
recalibration may proceed concurrently with regular production during
short breaks between cycles. Automatic Recalibration is triggered by
deformations, slight collisions, replacement of components or
exceedance
of predefined tolerances
of wear and tear.
- In combination with the calibrated robot, iSiOS
becomes a special purpose measurement system. iSiOS cell calibration automatically
identifies the precise 6D-pose - i.e. position and orientation - of fixtures and workpieces
in the robot workcell; e.g. the varying pose of
fixtures on a rotary table. The 3D-geometry of a robot tool or a
workpiece can be identified free of contact with a closely related
concept.
- iSiOS
gantry calibration
increases the absolute absolute accuracy of large gantry robots to
average
errors of a few hundreth mm. In demanding
applications
of the automotive industry, gantry robots
which are
constructed from standard off-the-shelve components are used as
high-precision CMM (coordinate measurement machines) after
calibration by iSiOS.
- iSiOS temperature compensation
offsets critical warm-up effects of robots. Depending on the robot
type, iSiOS
keeps maximum deviations below 0.1 mm during the whole operating period
The patented functional principle of iSiOS
uses the straightness of laser-beams for precise, model-based
calibration of robots. Robust sensors register the laser beam with high
accuracy. Traditional, costly precision measurement instruments are not
required anymore. A scalable sensitivity of the system guarantees
maximum absolute positioning accuracy of calibrated robots throughout
the complete workspace. After (re-)calibration, exact control of the
robot is achieved by updating the control unit without interrupting
regular production.
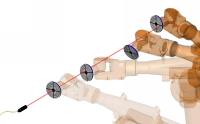
A closer look at iSiOS technology can be
found here.
A favourable price-performance ratio together with the compactness and
robustness of
components makes it possible to equip all critical robot cells
of a production line with a stationary iSiOS
system. Recalibration and object
measurement
capabilities are
readily available on site. The calibration proceeds automatically after
activation.
|
 |